Business Process Optimization: Complete Guide in 2025
This blog explores how business process optimization in 2025 drives operational efficiency, cost savings, and compliance through standardized workflows, automation, and real-time data insights. It provides a step-by-step guide and highlights how tools like Audit Now support continuous improvement across industries.
04 Jun 2025
•
Beril Işık
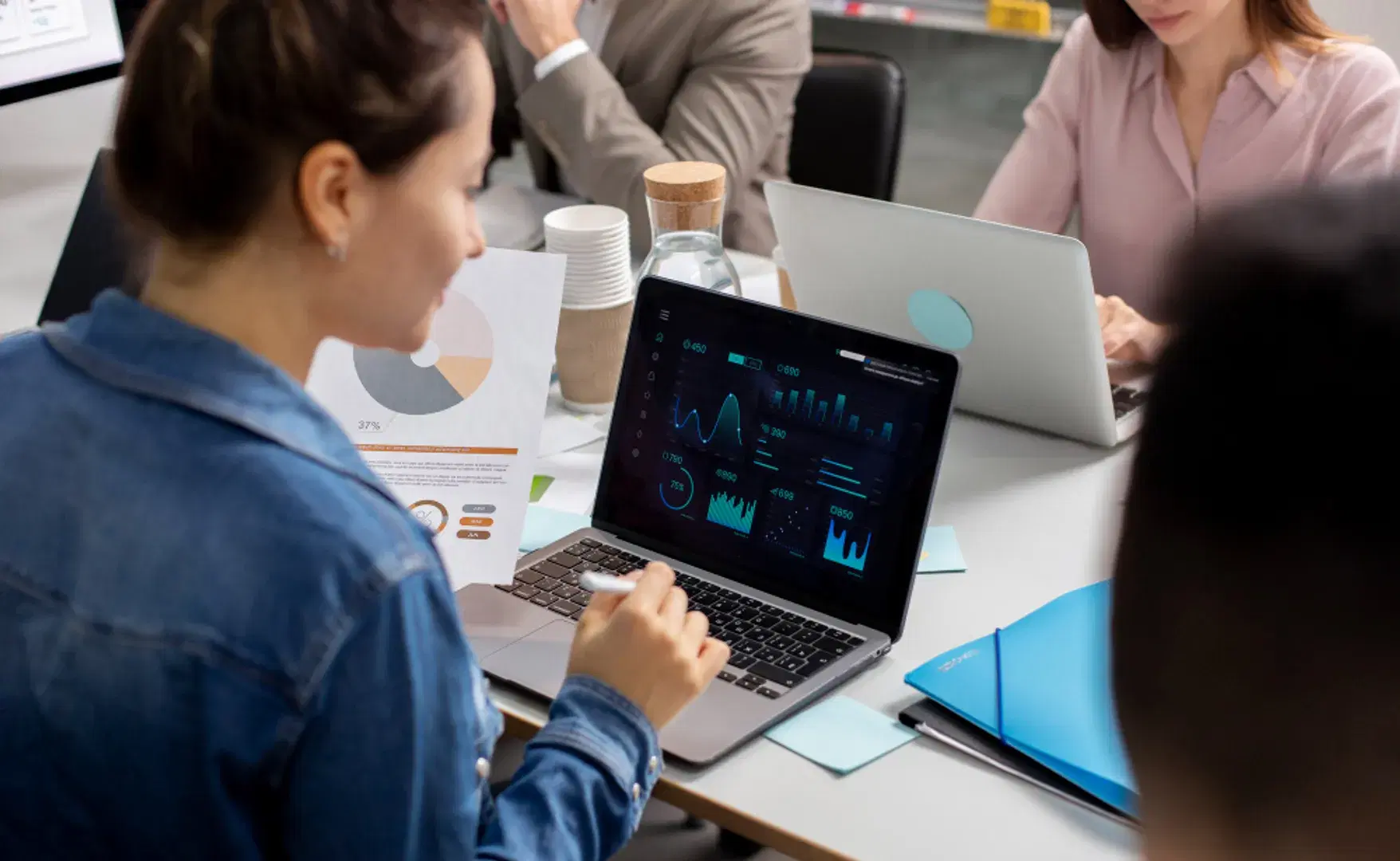
Featured Checklist
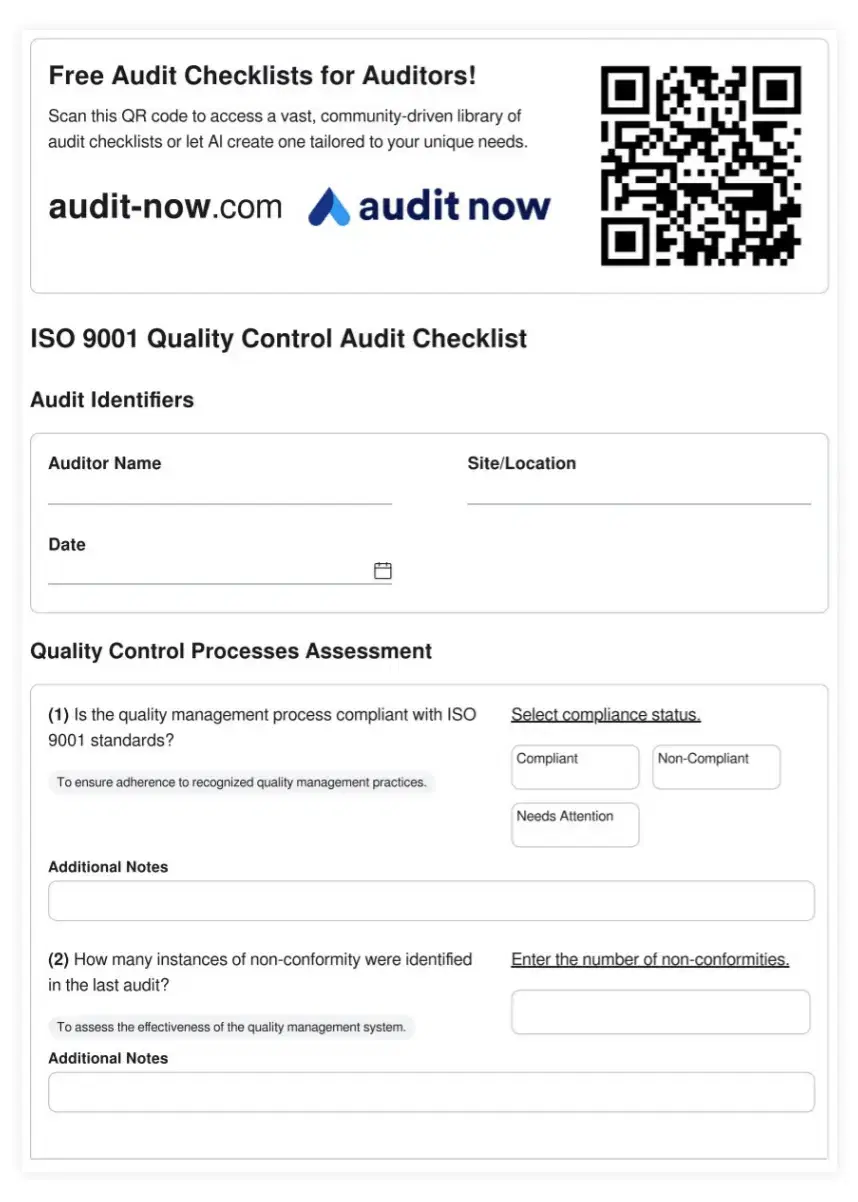
OSHA Process Safety Management (PSM) Mechanical Integrity Audit Checklist
Mechanical integrity is a critical element of Process Safety Management (PSM) in the chemical industry, ensuring that equipment and systems operate reliably and safely. This OSHA PSM Mechanical Integrity Audit Checklist is designed to evaluate compliance with the mechanical integrity requirements of OSHA's Process Safety Management standard (29 CFR 1910.119(j)). By assessing inspection, testing, and maintenance procedures for process equipment, this checklist helps identify potential weaknesses in mechanical integrity programs, enhance equipment reliability, and prevent catastrophic failures. Proper implementation of mechanical integrity protocols is essential for maintaining the safety and integrity of chemical processes, preventing releases, and protecting workers and the environment.
In today's competitive business landscape, process optimization has become essential for organizations seeking sustainable growth. Regardless of your industry, operational efficiency directly impacts profitability, compliance, and customer satisfaction.
But what exactly is business process optimization, and how can audit professionals and operations teams implement it successfully? I will explore process improvement strategies, workflow optimization techniques, and how digital tools can transform your operations in this blog.
What Is Business Process Optimization?
Process optimization refers to the systematic practice of analyzing, redesigning, and improving workflows to make them more efficient, cost-effective, and adaptable. This involves:
- Identifying operational bottlenecks
- Eliminating waste and redundancies
- Automating repetitive tasks
- Standardizing procedures across departments
- Implementing continuous improvement practices
For industries where compliance, safety, and consistency are critical, business process improvement can be the difference between scalable growth and operational chaos.
Why Business Process Optimization Matters in 2025
Many organizations operate with good intentions but rely on outdated or inefficient systems. Without streamlined processes, even high-performing teams struggle with delays, miscommunication, and redundant tasks.
Key Benefits of Process Optimization:
- Enhanced Operational Efficiency: Reduce time-to-completion by 30-50%
- Improved Resource Allocation: Optimize staff and budget distribution
- Higher Quality Outputs: Minimize errors through standardization
- Reduced Operational Risks: Proactive identification of potential issues
- Stronger Regulatory Compliance: Automated compliance tracking and reporting
- Cost Reduction: Studies show optimized processes can reduce operational costs by 15-25%
In audit-heavy industries, workflow optimization enables faster inspections, better documentation, and proactive issue resolution.
The Digital Transformation of Process Optimization
Traditional process audits relied on spreadsheets, printed checklists, and fragmented communication systems. This manual approach often resulted in scattered data across multiple platforms, creating silos that hindered comprehensive analysis. Version control became a constant challenge as teams worked with outdated documents and conflicting information. The lack of real-time visibility meant managers couldn't track progress or identify issues until it was too late, leading to delayed decision-making that impacted overall operational efficiency.
Modern process automation platforms like Audit Now are revolutionizing workflow optimization. With customizable digital checklists, AI-driven recommendations, and integrated reporting, teams can achieve continuous improvement without rebuilding from scratch.
Want to Reach Operational Excellence?
Tailor your checklists to match your team's daily processes. Start customizing now!
Try Now
5 Essential Areas for Effective Process Optimization
1. Standardization of Workflows and Checklists
Checklist standardization is one of the fastest ways to enhance operational efficiency. When every team follows identical procedures:
- Error rates decrease by up to 40%
- Training time reduces significantly
- Performance becomes measurable and comparable
- Quality consistency improves across all operations
2. Data-Driven Process Insights
Collecting real-time data from audit checklists enables you to:
- Analyze operational trends and patterns
- Identify recurring bottlenecks
- Make evidence-based improvements
- Track key performance indicators (KPIs)
Process monitoring tools provide managers with actionable insights to make faster, more informed decisions.
3. Strategic Task Automation
Process automation of recurring tasks delivers immediate benefits:
- Process automation of follow-up assignments
- Report generation and distribution
- Compliance notifications and reminders
- Data collection and analysis
This reduces administrative overhead by 60% and eliminates human error while freeing teams to focus on high-value strategic activities.
4. Cross-Functional Collaboration
Many operational inefficiencies stem from departmental silos. Optimized processes require:
- Shared tools and workflows
- Integrated communication systems
- Cross-departmental visibility
- Collaborative problem-solving approaches
Quality assurance, operations, compliance, and maintenance teams must work cohesively through unified platforms.
5. Continuous Improvement Culture
Business process optimization isn't a one-time project—it requires ongoing refinement. Successful organizations embed continuous improvement through:
- Regular process audits and reviews
- Version control and change logging
- Performance metric tracking
- Team feedback collection and implementation
Step-by-Step Process Optimization Implementation
Step 1: Comprehensive Current Process Audit
Begin with a thorough assessment of existing workflows:
- Document current processes using flowcharts or process maps
- Identify friction points, delays, and compliance gaps
- Measure baseline performance metrics
- Gather stakeholder feedback on pain points
Step 2: Define Clear Optimization Goals
Establish specific, measurable objectives:
- Cost Reduction: Target 15-20% operational cost savings
- Quality Improvement: Aim for 25% error reduction
- Time Efficiency: Reduce process completion time by 30%
- Compliance Enhancement: Achieve 95%+ audit pass rates
Step 3: Select the Right Digital Tools
Choose process optimization software that offers:
- Pre-built, customizable templates for your industry
- Real-time reporting and analytics
- Mobile accessibility for field operations
- Integration capabilities with existing systems
Platforms like Audit Now provide 10,000+ ready-made templates across multiple industries, accelerating implementation while ensuring consistency.
Step 4: Team Training and Change Management
Successful optimization requires team buy-in:
- Provide comprehensive training on new processes
- Communicate benefits clearly to all stakeholders
- Collect regular feedback during implementation
- Make processes feel like upgrades, not burdens
- Recognize and reward early adopters
Step 5: Monitor, Measure, and Optimize
Establish ongoing performance tracking:
- Set up real-time dashboards for key metrics
- Conduct regular process reviews
- Implement feedback loops for continuous improvement
- Schedule quarterly optimization assessments
Common Process Optimization Challenges and Solutions
- Resistance to Change: Communicate benefits clearly and involve end-users in redesigning processes.
- Tool Overload: Avoid using multiple disconnected platforms. Choose tools that integrate audit management, checklists, and reporting.
- Lack of Real-Time Visibility: Real-time dashboards and mobile-friendly audit tools bridge this gap.
FAQ
How long does process optimization typically take?
Most organizations see initial improvements within 30-60 days, with full optimization achieved in 3-6 months depending on complexity.
What's the average ROI of process optimization?
Studies indicate ROI ranges from 200-400% within the first year through cost savings and efficiency gains.
Can small businesses benefit from process optimization?
Absolutely. Small businesses often see the most dramatic improvements due to their agility and ability to implement changes quickly.
How do you measure process optimization success?
Key metrics include cycle time reduction, error rate decrease, cost per process, employee productivity, and customer satisfaction scores.
Guides: Learn More