Process Improvement Specialist Checklists
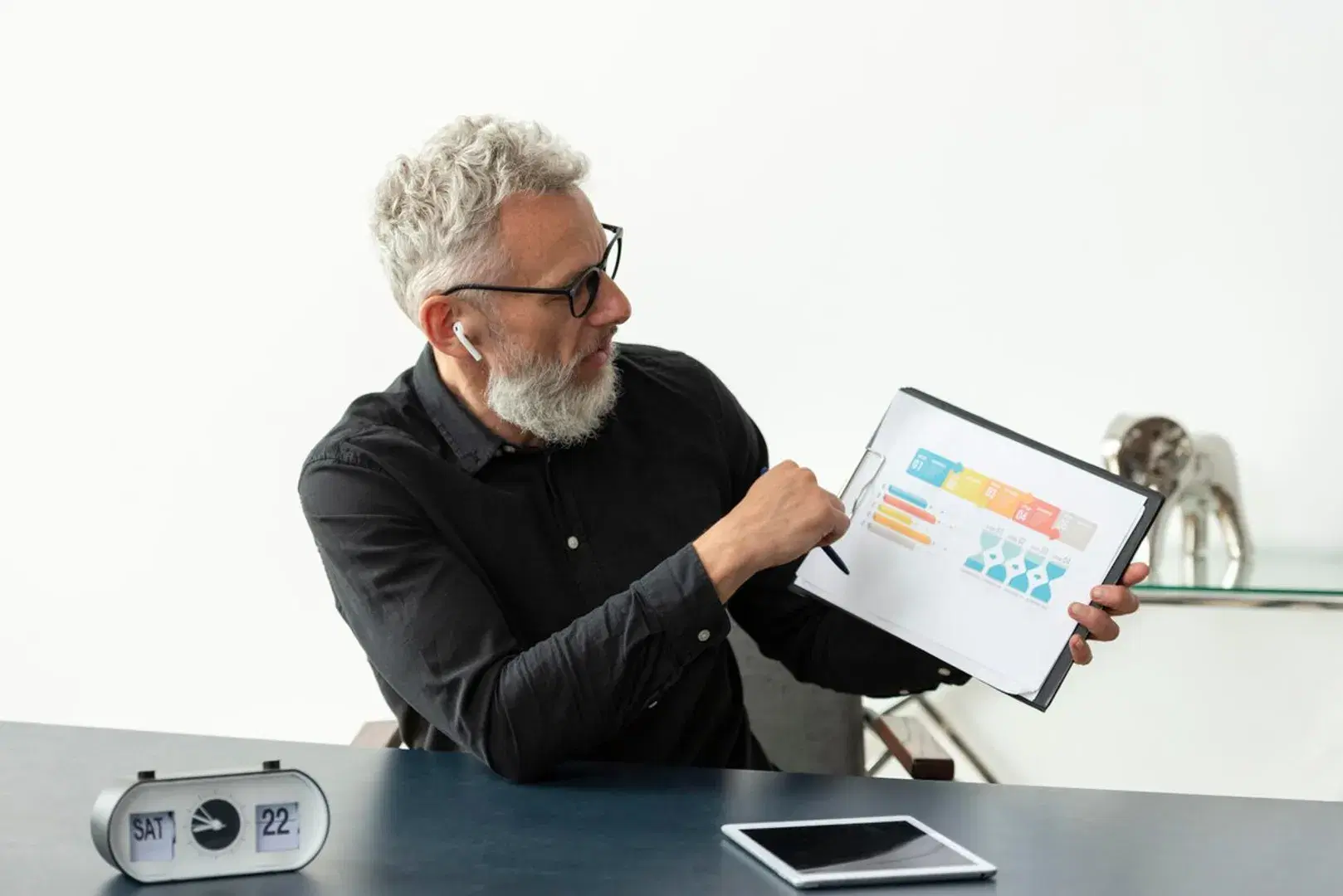
Process Improvement Specialist Operational Overview
Process improvement specialists face many challenges in their daily work. They must find ways to make operations run smoother and more efficiently. This often means looking at complex systems and figuring out where things can be done better.
When processes aren't working well, it can hurt the whole business. Products might not meet quality standards. Customer service could suffer. Costs may go up. Process improvement specialists help fix these issues. They look at how work is done and find ways to do it faster, cheaper, or with fewer mistakes.
Quality management is a big part of process improvement. Specialists need to make sure that as processes change, quality stays high or gets even better. This takes careful planning and checking. That's where auditing comes in.
Core Audit Requirements & Checklist Importance
Audits are key tools for a process improvement specialist. They help find problems and track progress. A good audit looks at all parts of a process. It checks if rules are being followed and if work is being done right.
Checklists make audits more thorough and consistent. They remind auditors what to look for and help them not miss anything important. With a good checklist, different people can do the same audit and get similar results. This makes the findings more trustworthy.
Many industries have rules about how processes should work. Audits help show that a company is following these rules. This can be important for safety, legal reasons, or keeping customers happy.
- Process documentation: Check if all steps are written down clearly
- Employee training: Make sure workers know the right way to do things
- Equipment maintenance: Check if machines are working properly and safely
- Quality control measures: Look at how product quality is checked
- Data collection: See if the right information is being gathered and used
Lean Six Sigma in Process Improvement
Lean Six Sigma is a popular method in process improvement. It combines ideas from Lean manufacturing and Six Sigma quality control. The goal is to remove waste and reduce variation in processes. This leads to more consistent, high-quality results.
One key idea in Lean Six Sigma is the DMAIC cycle. This stands for Define, Measure, Analyze, Improve, and Control. Process improvement specialists use this step-by-step approach to tackle problems. They start by clearly stating what needs to be fixed. Then they gather data, figure out root causes, make changes, and set up ways to keep the improvements going.
Another important tool is value stream mapping. This involves drawing out all the steps in a process. It helps show where delays or waste happen. Process improvement specialists use these maps to find bottlenecks and areas for improvement. They can then suggest changes to make the whole process flow better.
Ask the Experts
Have questions about Lean Six Sigma? Contact our experts for free advice!
Contact
Continuous Improvement and Change Management
Process improvement isn't a one-time thing. It's ongoing. Specialists need to create a culture of continuous improvement. This means always looking for ways to do things better, even when processes seem to be working fine. Small, regular improvements can add up to big gains over time.
Change management is a crucial skill for process improvement specialists. When processes change, people's jobs often change too. This can cause stress or resistance. Good change management helps workers understand why changes are happening and how to adapt. It includes clear communication, training, and support throughout the change process.
Measuring performance is key to continuous improvement. Process improvement specialists set up metrics to track how well changes are working. These might include things like cycle time, defect rates, or customer satisfaction scores. By watching these numbers, they can see if improvements are having the desired effect and where more work is needed.
Digital Transformation with Audit Now
Modern technology can make process improvement work easier and more effective. Audit Now offers digital tools that streamline auditing and improvement efforts. Our AI-powered checklists adapt to your specific needs. They learn from past audits to suggest relevant questions and areas to check.
With Audit Now, teams can work together in real time, no matter where they are. Findings can be shared instantly, speeding up the improvement process. Our template library gives you a head start, with best-practice checklists for many industries and processes. You can use these as-is or customize them to fit your unique needs.
Ready to take your process improvement efforts to the next level? Check out our template library at audit-now.com/templates/. And don't forget to try our AI checklist generator at audit-now.com/generate-ai-checklist/ to create custom checklists tailored to your specific processes.
Most Popular 10 Process Improvement Specialist Checklists
ISO 9001 Risk Management Audit Checklist
ISO 9001 Internal Audit Process Checklist
Lean Manufacturing Audit Checklist
CMMI Process Area Audit Checklist
5S Implementation Checklist for Quality Management
Maintenance Management Assessment Checklist
DO-254 Hardware Tool Qualification Checklist