Quality Control Analyst Checklists
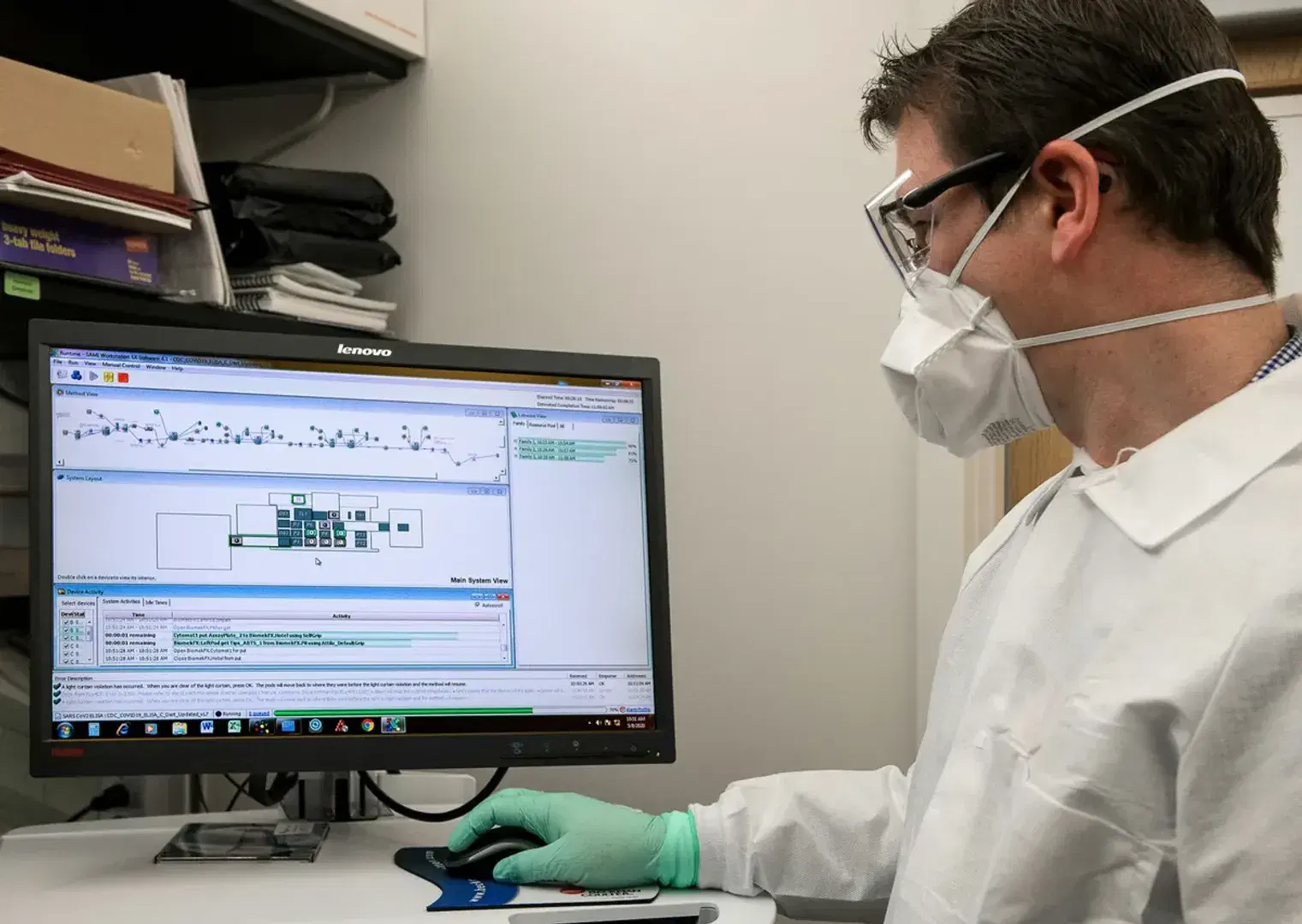
Featured Checklist
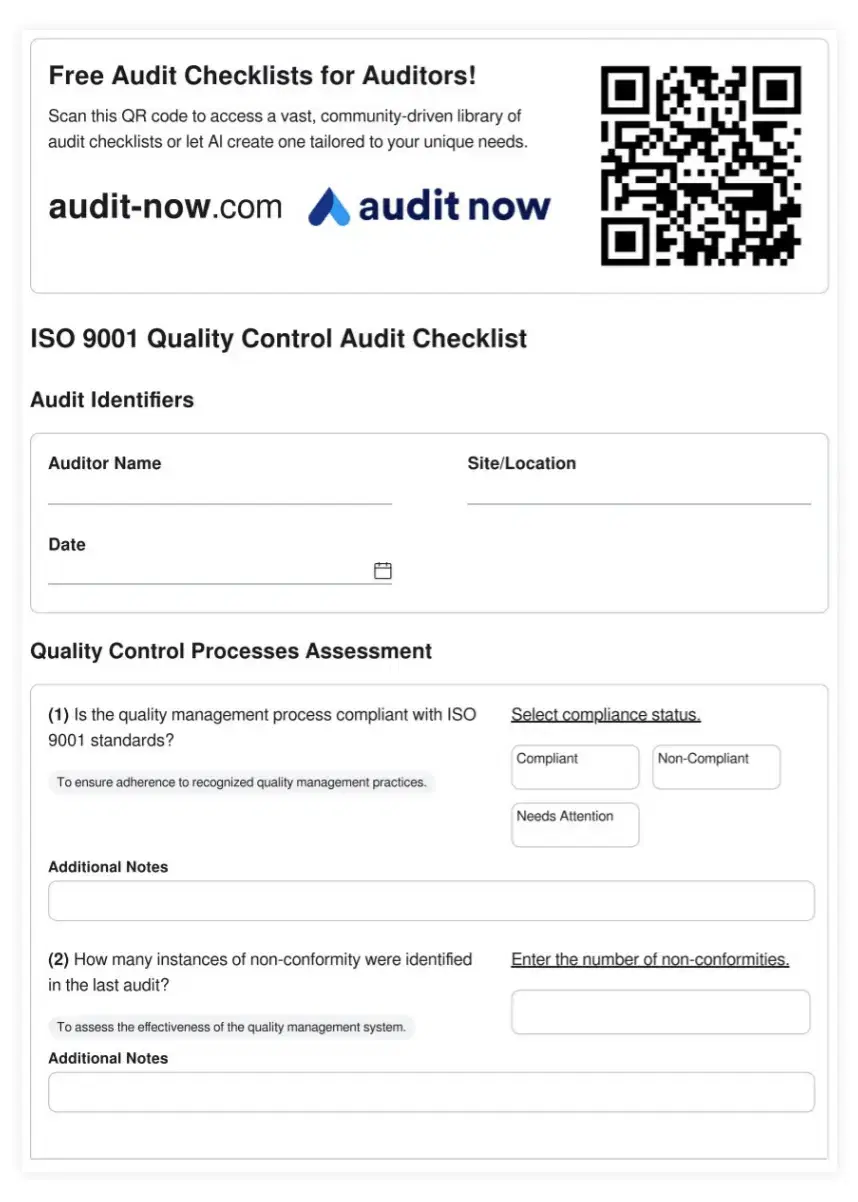
GMP Quality Control Laboratory Audit Checklist
Quality Control (QC) laboratories play a pivotal role in ensuring the safety, efficacy, and quality of pharmaceutical products. This GMP Quality Control Laboratory Audit Checklist is an essential tool for evaluating compliance with Good Manufacturing Practice (GMP) standards in pharmaceutical QC labs. It addresses critical aspects of laboratory operations, including testing procedures, equipment calibration, data integrity, and sample management. By systematically assessing these areas, this checklist helps identify potential gaps in QC processes, mitigate risks associated with inaccurate test results, and maintain the highest standards of analytical excellence. Implementing this checklist supports pharmaceutical companies in enhancing their quality assurance efforts and maintaining regulatory compliance.
Quality Control Analyst Operational Overview
Quality Control Analysts face many challenges in their day-to-day work. They must ensure products meet high standards while dealing with tight deadlines and changing requirements. Balancing speed and accuracy is a constant struggle, as is keeping up with new regulations and industry best practices.
These challenges directly impact a company's bottom line. Poor quality control can lead to product recalls, customer complaints, and damage to the brand's reputation. On the flip side, effective quality control helps build customer trust, reduces waste, and improves overall efficiency.
Quality management is at the heart of a Quality Control Analyst's role. It involves setting standards, monitoring processes, and continuously improving procedures. This leads us to the critical importance of auditing in maintaining and enhancing quality control measures.
Core Audit Requirements & Checklist Importance
Audits are essential for Quality Control Analysts to assess and improve their processes. They help identify gaps, ensure compliance, and drive continuous improvement. Key components of an effective audit include thorough documentation review, on-site inspections, and interviews with relevant personnel.
Systematic checklists play a crucial role in the audit process. They provide a structured approach, ensuring no important aspects are overlooked. Checklists also promote consistency across different auditors and audit cycles, making it easier to compare results over time and across different departments or locations.
Compliance requirements often drive the need for regular audits. These may come from industry standards, government regulations, or internal company policies. By using well-designed checklists, Quality Control Analysts can ensure they meet all necessary compliance criteria.
- Product Specifications: Verify products meet design and performance requirements
- Process Controls: Check that manufacturing processes are consistent and well-documented
- Testing Procedures: Ensure all required tests are performed and results are properly recorded
- Documentation: Review all quality-related documents for accuracy and completeness
- Corrective Actions: Assess the effectiveness of actions taken to address previous issues
Manufacturing Industry Challenges
In the manufacturing industry, Quality Control Analysts face unique challenges. They must deal with complex supply chains, varying raw material quality, and the need to maintain consistency across large production runs. Ensuring product safety and reliability is paramount, especially in industries like automotive or aerospace where failures can have serious consequences.
Best practices in manufacturing quality control include implementing statistical process control (SPC), using automated inspection systems, and maintaining detailed traceability records. Regular equipment calibration and maintenance are also crucial to ensure consistent product quality.
Quality control measures in manufacturing often involve a combination of in-process checks and final product inspections. This might include dimensional checks, functional testing, and destructive testing of sample units. Advanced techniques like X-ray inspection or ultrasonic testing may be used for critical components.
Optimizing Quality Control Processes
Process optimization is key to improving quality control efficiency. This might involve streamlining inspection procedures, implementing lean manufacturing principles, or using data analytics to identify trends and potential issues before they become problems. For example, a Quality Control Analyst might use control charts to monitor key process parameters and quickly detect when a process is drifting out of specification.
Risk management is another important aspect of quality control. This involves identifying potential quality risks, assessing their likelihood and impact, and implementing measures to mitigate them. For instance, a Quality Control Analyst might implement more frequent inspections for components from a new supplier until they've proven their reliability.
Performance metrics help track the effectiveness of quality control efforts. Common metrics include defect rates, first-pass yield, and customer complaint rates. By regularly reviewing these metrics, Quality Control Analysts can identify areas for improvement and measure the impact of their quality initiatives.
Digital Transformation with Audit Now
Audit Now offers AI-powered checklists that revolutionize the quality control process. These smart checklists learn from your audit history, suggesting improvements and highlighting potential issues before they occur. Real-time collaboration features allow multiple team members to work on audits simultaneously, streamlining the process and ensuring everyone is on the same page.
With Audit Now's extensive template library, you can quickly create customized checklists tailored to your specific quality control needs. Whether you're in manufacturing, healthcare, or any other industry, you'll find templates that align with your requirements and best practices.
Ready to transform your quality control audits? Visit audit-now.com/templates/ to explore our comprehensive checklist templates. And don't forget to try our AI checklist generator at audit-now.com/generate-ai-checklist/ to create custom checklists tailored to your unique needs.